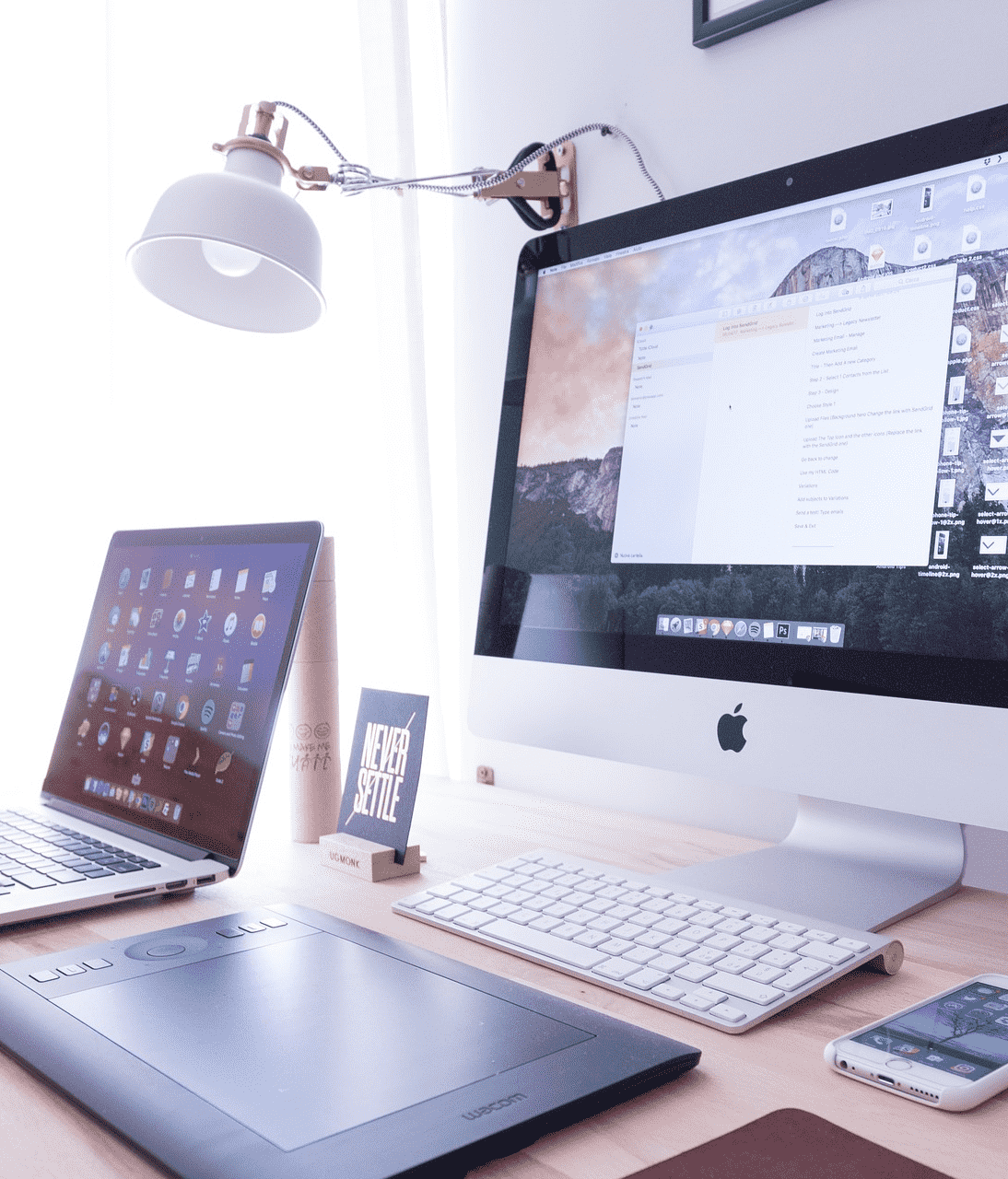
Equipment Uptime & Peace of Mind
On average, downtime can cost manufacturers up to $260,000 per hour, according to Aberdeen Research.
process control
As a die casting manufacturer, you commute to the factory daily, work from home and monitor the operation remotely, or wait by the phone for critical news.
on time deliveries
You have the same worries about making daily delivery commitments knowing there are so many things that can go wrong on the manufacturing floor
be proactive
Identify, measure, and improve all of your unique die cast processes by outfitting them with HIGHLY EFFECTIVE Visi-Trak predictive maintenance systems.
easy to install
We take care of selecting and installing all the technology – all the machine owner has to do is prioritize the data.
Eliminate the Guesswork
Machine failures create chaos, confusion, stress, and problems. The good news is your process is under your control with Visi-Trak.
PREDICT FAILURES BEFORE THEY OCCUR
Our PdM tools increase uptime by providing capability in four unique areas: Predictive Maintenance Data, Spare Parts, Qualified People, and Knowledge to prevent problems.
TAKE PROACTIVE MEASURES
Identify, measure, and improve all of your unique die cast processes by outfitting them with HIGHLY EFFECTIVE Visi-Trak predictive maintenance systems.
What Is Predictive Maintenance (PdM)?
PdM is a technology system that continuously monitors parameters on a machine, transmits the measurements remotely, and analyzes the data with software. When the software determines that a failure is likely, it warns the maintenance staff so they can schedule a repair when it will have the least impact on production outputs.
The REAL Cost of Scrap
Why You Need Predictive Maintenance.
Process Variation
Process Variation is the primary cause for scrap. If all your castings have the same issue, then it is a design or process problem.
Equipment Variation
However, if 90 of 100 parts are good, something in the process is changing enough to fall outside of the quality window.
Process Capability
10% Scrap = 10% variation. This variation can be discovered by monitoring and archiving every shot with a process monitoring system.
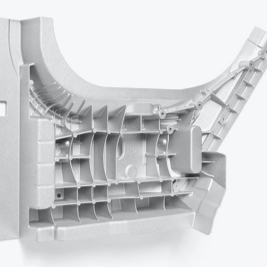
Typical Die Casting Defects
Scrap = parts produced that cannot be sold. Once the casting process is established to make good castings, something (or several things) changes in the process resulting in defective castings. Scrap Rate = bad castings per hour / shots per hour.
example
Ex. Making 40 castings per hour. If 6 per hour are scrap = 15%. If castings can be sold at $5 ea – $5×6/hr = $30 per hour loss. If 2 x 10hr shifts = 20hrs x $30 = $600/day loss
scrap rate
A scrap rate of 15% and your annual sales revenue is $10,000,000 the lost opportunity is $1,500,000.
die casting example
Scenario
If a die caster with 10 machines reduced scrap from 15% to 5%, it will reduce the total number of die casting machine hours needed to make the same amount of good parts.
scrap rate
Reducing the scrap from 15% to 5% increases capacity equal to adding another DCM.
die cost
If your die cost $200,000 and this cost is typically amortized over 100,000 pieces ($200k/100k), it adds $2.00 to the cost of each part.
die life cycle
Scrap also reduces the lifetime of the die; and increases the cost per good casting made.
production cost
At 15% scrap, the cost for each part increases from $2.00 to $2.35